Deep Hole Drilling
Deep hole drilling is economically used for boreholes more than ten times deeper than their diameter. It is a challenging machining process due to its high length-to-diameter ratio. Depending on the required hole diameter, different methods are used. Single lip drills are typically used for smaller diameters than 80 millimetres, whereas ejector drilling with a double-tube system is used for larger diameters. Deep hole drilling applications can be found in medical technology, textile, automotive, and plastics industries.
Single-lip Deep Drilling
Single-lip deep hole drills have an asymmetrical tool design with a single cutting edge. The asymmetrical design leads to the self-centring of the tool in the bore by guide pads, constantly burnishing the borehole surface and improving the surface quality. The machined chips are evacuated through a single V-shaped channel along the tool's shaft. Unlike twist drills, the chip evacuation is solely archived by the cutting-fluid flow, as the single channel does not as an Archimedean screw. Therefore, single-lip drills have a higher clogging tendency in the case of suboptimal chip forms, which leads to early tool breakage.
Research Topics
The research activities at ITM in the field of deep hole drilling range from developing simulation methods and their coupling for the modelling of the deep hole drilling process to the analysis of drill design modifications to improve the fluid distribution around the cutting edge and chip evacuation.
Why Mesh-free Simulation Methods?
The dynamic modelling of the large motion of the chips during their evacuation and the surrounding fluid flow would lead to distorted meshes in mesh-based simulation methods like the Finite Element Method or Finite Volumen Method. The distorted mesh leads to numerical problems. Consequently, repeated re-meshing would be required during the chip transport, which is error-prone and computationally expensive.
As an alternative, mesh-free simulation methods, like Smoothed Particle Hydrodynamics for describing the fluid flow and the Discrete Element Method for the chips, the drill, and the borehole, are better suited. Smoothed Particle Hydrodynamics is a Langrangian method which describes the fluid flow based on moving interpolation points. This enables the modelling of many problems, like non-regular moving free surfaces or dynamic fluid-structure interaction.
Fluid Distribution and Chip Evacuation
Earlier investigations of the fluid flow of single-lip drills showed that the cutting fluid gets trapped on the backside of the cutting edge. Furthermore, the chip form, created by the standard drill design, offers little resistance for cutting fluid flow leading to a suboptimal chip evacuation. Consequently, the standard design has significant potential for improvement of fluid distribution and chip evacuation. For example, an acceleration of the chip evacuation speed by 60% was archived by a different chip form due to a modified cutting edge in combination with an improved cross-section of the cooling channel.
Chip Jamming and Drill Breakage
The single-lip drill has an increased clogging tendency in the case of suboptimal chip forms because of its single straight chip channel, which leads to early tool breakage. Therefore, one of the current research topics is modelling an artificial chip jamming to investigate the fluid flow in these scenarios and the forces and torques on the drill. Early results can be seen in the video below.
Ansprechpartner
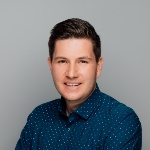
Andreas Baumann
M.Sc.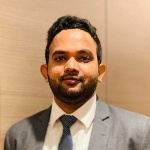
Nuwan Rupasinghe
M.Eng.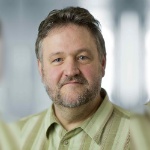
Peter Eberhard
Prof. Dr.-Ing. Prof. E.h.- Profile page
- +49 711 685 66388
- Write e-mail
- Pfaffenwaldring 9, 70569 D-Stuttgart