Discrete Element Method
The Discrete Element Method (DEM) simulates the behavior of granular materials – like sand, gravel, and powders – by treating them as individual, interacting particles.
Programm Features
Periodic boundary conditions are an important tool for the simulation of space with unlimited extend that is continuously filled with matter of a specific type. The example shows a simple simulation with 3D periodic boundary conditions and Pasimodo's contact model for non-convex polyhedral geometries.
For a better perception of the periodicity of the simulation domain, it can be useful to concentrate on the red torus while viewing the video in a loop.
Granular Media
Identification of the piling angle of glass beads. To allow for a better perception of the rotation, the beads are colored with a checkered color pattern. The simulations consider sticking friction, slipping friction and drilling friction and, moreover, the rolling resistance of the glass beads.
Simulations of a double lane change maneuver of a single-compartment tank truck carrying a granular cargo. The simulations were performed as co-simulations between Pasimodo (granulate) and Simpack (multibody system of the truck) with a data exchange via Matlab/Simulink and TCP/IP connections. The maneuver is depicted with a track velocity of v=17.5 m/s on the left and a track velocity of v=20 m/s on the right.
Smoothed Particle Hydrodynamics (SPH)
SPH is a mesh-free simulation technique that represents a continuum as individual "particles" with properties like velocity and density. Unlike grid-based methods, SPH particles move freely, making it ideal for simulations involving significant changes in shape or complex interfaces. This makes it particularly strong for modeling phenomena like hydrodynamics, fluid-structure interactions, and material fracture.
Thermal Modeling
Left: Simulation of deep penetration laser welding of aluminum. The grey particles form the solid material, the blue particles form the liquid weld pool, and the light grey particles show the resolidified material. Evaporation is considered through recoil pressure on the liquid melt, the gas phase is currently not modeled.
Right: Simulation of deep penetration laser welding of ice. On the left, the light grey particles form the solid ice block and the blue particles form the liquid weld pool (water). Evaporation is considered through recoil pressure on the liquid melt, the gas phase is currently not modeled. On the right, the absorbed intensities (max: red, min: blue) from the laser beam at the capillary front are visualized using a ray-tracing scheme developed at the IFSW.
Elastic Materials
A notched sample (CT test, DIN EN ISO 12737) of aluminium is pulled asunder above and below the notch. The particles are coloured according to either damage from 0 (undamaged) to 1 (completely damaged) or von Mises tension.
SPH simulation of an orthogonal cutting process for different materials:
left and center: heat-treated steel C45E with a cutting speed of 1.6 m/s (blue = low von Mises equivalent stress; red = high von Mises equivalent stress)
right: aluminium alloy AlMg3 with a cutting speed of 1.6 m/s using adaptive particle resolution (blue = original particles; red = refined particles)
Complex Liquid Interactions
Simulation of immiscible fluids with different densities
left: breaking dam scenario
right: a Rayleigh-Taylor instability, which occurs at the interface between two fluids of different densities when the fluids are accelerated against each other
Fluid-Structure Interaction coupling SPH and DEM
Preliminary SPH-Simulation of the Cooling-Lubricant Supply for Deep-Hole Twist-Drills
(top: different dynamic viscosities and NCP-interaction test, bottom: viscous as water).
Simulation with Pasimodo and Visualisation with Paraview by Dirk Schnabel in cooperation with Dr.Ing Ekrem Oezkaya and Prof. Dr.Ing Dirk Biermann, both Institute for Machining Technology (ISF), TU Dortmund.
SPH-Simulation of the Cooling-Lubricant Supply for Single-Lip Deep-Hole Drilling-Processes using glyph visualization and recomputed liquid surface.
Simulation with Pasimodo and Visualisation with Paraview by Dirk Schnabel in cooperation with Dr.Ing Ekrem Oezkaya and Prof. Dr.Ing Dirk Biermann, both Institute for Machining Technology (ISF), TU Dortmund.
Hybrid Discrete Element Method
Pasimodo is highly flexible. Its plugin structure allows its easy extension for new challenges. The following videos show some of the extensions developed in the past.
Ballast made from bonded particles is subjected to different loadings:
1. Cyclic compression.
2. Oedometric compression. (Firstly, all particles are shown in the movie. Subsequently, only those particles are displayed, which are involved in fracture processes.)
3. A sleeper is pressed into a ballast bed.
Model creation by Christian Ergenzinger in the framework of the DFG SFB 716.
Contact
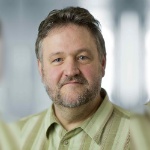
Peter Eberhard
Prof. Dr.-Ing. Prof. E.h.- Profile page
- +49 711 685 66388
- Write e-mail
- Pfaffenwaldring 9, 70569 D-Stuttgart
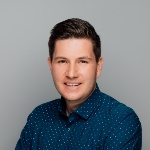